En este proceso el electrodo es un alambre revestido,
donde el soldador controla el proceso manualmente sobre la longitud y
dirección del arco que se establece entre el extremo del electrodo y la
pieza a soldar (metal base).
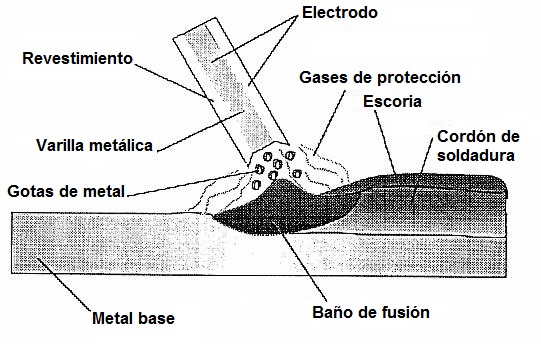
El calor generado por el arco eléctrico funde el
revestimiento y la varilla metálica del electrodo, a la vez que la
combustión del revestimiento sirve para crear una atmósfera protectora
que impide la contaminación del material fundido.
Las gotas de metal fundido procedente de la varilla
metálica del electrodo van a depositarse en el baño de fusión. A la vez,
el material procedente de la fusión del revestimiento del electrodo
genera una escoria, que por viscosidad flota sobre el baño de fusión,
protegiéndolo contra un enfriamiento rápido y de la contaminación del
aire circundante.
Una vez frío el cordón se procede a eliminar la escoria que queda como una especie de costra sobre la superficie del cordón.
Además de las funciones de protección del baño de
fusión, el recubrimiento del electrodo desempeña otras funciones, entre
las que están las siguientes:
• Debido a que el recubrimiento exterior no se
quema tan rápido como el alambre del electrodo, genera una especie de
cráter en la punta del electrodo que permite concentrar la salida del
arco, controlando mejor la dirección del arco, lo que permite también
poder soldar en varias posiciones, además de mejorar la eficiencia de la
soldadura y disminuir las pérdidas de energía.
• Debida a la composición química del
revestimiento, éste permite mejorar el cebado y estabilizado del arco,
motivado por la presencia en su composición de sales de sodio y potasio
que garantizan la presencia de iones positivos durante el proceso de
soldadura.
• Como el alambre del electrodo no siempre será
de la misma composición que el metal base, el decapante que constituye
el recubrimiento permite aportar aleaciones al metal de soldadura que
mejoren las características mecánicas del cordón.
• Como ya se ha dicho, durante el quemado del
recubrimiento del electrodo se origina una envolvente gaseosa que
permite desalojar al oxígeno y al nitrógeno del metal fundido, evitando
la oxidación del cordón de soldadura.
• Además, como también se ha dicho, el
recubrimiento del electrodo genera una capa de escoria que queda
depositada sobre el baño de fusión protegiéndolo de la contaminación
atmosférica mientras el baño está fluido y regulando su velocidad de
enfriamiento, dando como resultado un cordón más óptimo en resistencia
mecánica y frente a la corrosión.
Los electrodos para la soldadura manual por arco
revestido se seleccionarán, primero en función del metal base a soldar, y
después de acuerdo con el tipo de recubrimiento. En principio, el tipo
de alambre del electrodo a utilizar será de una aleación, al menos igual
en composición al del metal base, o si puede, más alta.
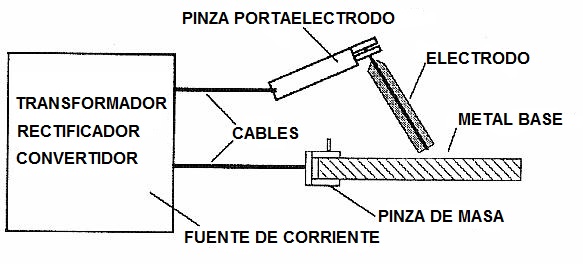
Aunque en el apartado 4.3 de este tutorial se expone
con más detalle los diferentes tipos de electrodos más empleados en los
aceros inoxidables, a continuación se expondrá algunos aspectos
generales para los electrodos más comúnmente usados en el procedimiento
de soldadura manual por arco revestido.
La composición química del recubrimiento empleado en
el electrodo influirá en aspectos tales como las posiciones admisibles
de soldeo o la forma y uniformidad del cordón de soldadura.
La norma AWS reconoce dos grandes familias de electrodos especiales, designados mediante los sufijos -15 y -16 que se incluyen al final en la designación del electrodo.
Los terminados en -15 son electrodos de óxido
de calcio o tipo básico, que se usan con corriente continua polaridad
inversa (CCPI). Generan soldaduras limpias, con bajo contenido de
nitrógeno, oxígeno e inclusiones. Las soldaduras realizadas con estos
electrodos ofrecen una buena resistencia a la rotura, son dúctiles y
tienen la mejor resistencia a la corrosión. Estos electrodos tienen
buena penetración y se pueden usar en todas las posiciones, lo cual es
deseable en los trabajos de montaje.
Por otro lado, el recubrimiento de los electrodos tipo -16
generalmente tiene una mezcla de óxidos de calcio y titanio y se usan a
menudo con corriente alterna. Son más populares que los del tipo -15
debido a sus mejores características de operación. El arco es estable y
uniforme, con una buena transferencia de metal. El cordón de soldadura
es uniforme, con un contorno entre plano y ligeramente cóncavo. La
escoria se elimina fácilmente sin que quede un film secundario en el
cordón de soldadura.
A continuación, se exponen algunas recomendaciones a
tener en cuenta en la soldadura manual por arco con electrodo revestido
en los aceros inoxidables:
.
• Almacenamiento y manejo de electrodos: una
vez abierto el paquete de electrodos, estos deben conservarse a la
temperatura que indique el fabricante, generalmente suele ser una
temperatura de almacenamiento de 110 ºC. Si los electrodos han estado
expuestos a humedad, entonces deberán ser reacondicionados calentándolos
hasta unos 260 ºC para eliminar la humedad del recubrimiento.
La presencia de humedad en los electrodos que van a
ser empleados en la soldadura de aceros inoxidables es altamente
perjudicial, dado que el hidrógeno generado puede producir porosidad en
la soldadura. Además, en el caso de aceros inoxidables dúplex, la
humedad genera el riesgo añadido de sufrir de gran fragilidad por
hidrógeno en el cordón de soldadura.
La humedad en el recubrimiento no es la única causa de
porosidad en la soldadura, la presencia de restos de pinturas o grasa
en los bordes de las piezas a soldar también puede generar porosidad.
En el caso de presentarse los electrodos mojados, estos deberán ser automáticamente descartados.
• Intensidad de corriente: aunque los
fabricantes suelen indicar los rangos de corriente a emplear con los
electrodos para cada diámetro, al tener los aceros inoxidables una mayor
resistencia eléctrica que los aceros ordinarios, los rangos de
intensidad de corriente que se necesiten para soldar los aceros
inoxidables supondrá un aumento del orden del 25 al 50% respecto a los
necesarios para soldar acero común.
• Encendido y apagado del arco: el
establecimiento del arco deberá realizarse en un punto de la junta de
soldadura de manera que el metal depositado en el establecimiento del
arco se vuelva a fundir.
Tampoco se recomienda extinguir de forma abrupta el
arco, lo que dará lugar a cráteres. Para evitar esto, se recomienda
mantener al final el arco unos momentos sobre la soldadura y luego
moverlo rápidamente hacia atrás a la vez que se va alzando el arco del
cordón hasta que éste se extingue.
• Evitar realizar excesivos movimientos de
oscilación con el electrodo, pues podrá dar lugar a un aporte excesivo
de calor sobre el cordón que puede causar fisuras o deformaciones en la
soldadura.
El proceso TIG (Tungsten Inert Gas) resulta un
procedimiento muy adecuado para soldar el acero inoxidable. En este
caso, el arco eléctrico se establece entre un electrodo no consumible de
Tungsteno y el metal base, bajo una atmósfera protectora generada por
un gas inerte.
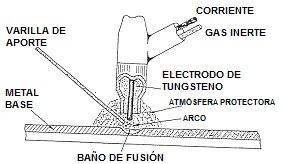
El gas inerte (normalmente argón) se usa para proteger
del aire circundante al metal fundido de la soldadura. Si es necesario,
también se puede agregar metal de aporte en forma de un alambre o
varilla que se introduce dentro del arco, de forma bien manual o
automáticamente, para fundirlo y cuyas gotas caigan dentro del baño de
fusión.
El procedimiento de soldadura TIG genera cordones de
gran calidad, sin escorias (dado que emplean electrodos no consumibles
sin revestimiento), ni proyecciones, por lo que se usa para soldaduras
de responsabilidad en acero inoxidable, donde obtener soldaduras de
calidad sea necesario.
Generalmente el procedimiento TIG se suele emplear
para soldar piezas de poco espesor (hasta 6 mm. aproximadamente), dado
que para espesores de piezas mayores de 6 - 7 mm este procedimiento no
resulta económico. De esta manera, para espesores mayores a los 6 mm.,
se suele emplear procedimientos de soldadura por arco sumergido.
Entre las ventajas que presenta este procedimiento están las siguientes:
• No genera escorias en el cordón, lo cual reduce las tareas de limpieza posterior a la soldadura.
• Es un proceso que se puede emplear en todas
las posiciones de soldadura, lo cual lo hace especialmente recomendable
para la soldadura de tubos y cañerías.
• No genera salpicaduras alrededor del cordón.
• Afecta muy poco a la composición química y propiedades del metal base durante el proceso de soldadura.
- Equipamiento para la soldadura TIG:
Para soldar aceros inoxidables mediante procedimiento
TIG se debe emplear corriente continua con polaridad directa (electrodo
conectado al negativo).
Asimismo, para soldar en TIG se recomienda emplear
como fuente de energía un equipo de alta frecuencia que permita iniciar
la soldadura y establecer el arco sin necesidad de tener que tocar con
el electrodo la pieza, con ello se evita la contaminación tanto del
metal base como del electrodo.
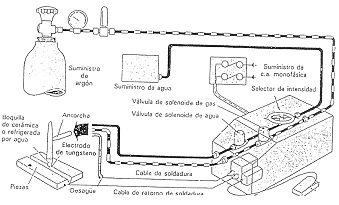
También se recomienda que el equipo de soldeo disponga
de un dispositivo de control, un pedal por ejemplo, cuyo accionamiento
permita regular el nivel de intensidad de corriente que suministra el
equipo. Con ello el operario podrá aumentar o disminuir la intensidad de
corriente en función de las condiciones de trabajo de la soldadura.
Esto es especialmente útil en los momentos finales de
la soldadura, porque de esta forma se conseguirá un apagado gradual del
arco conforme se va reduciendo progresivamente la intensidad de
corriente. Con ello, se logra disminuir el tamaño del baño de fusión y
evitar la formación de grietas al final del cordón.
En caso de no disponer de un equipo de control de la
fuente que permita reducir la intensidad de corriente en los momentos
finales de la soldadura, se recomienda, como alternativa, aumentar la
velocidad de avance en los últimos tramos de soldadura para así
conseguir disminuir el tamaño del baño de fusión.
- Consumibles:
Como gas protector para soldar aceros inoxidables
mediante procedimiento TIG se suele utilizar argón puro, helio o una
mezclas de ambos. En la soldadura manual y de chapas con espesores
menores de 1,6 mm se recomienda emplear argón como gas de protección.
Por el contrario, el helio produce un mayor flujo calorífico y una
penetración más profunda, lo cual puede ser una ventaja en algunas
operaciones de soldadura automática. Las mezclas de argón-helio pueden
mejorar el contorno de la soldadura y la mojabilidad.
También se suele usar una mezcla de argón-hidrógeno en
la soldadura de inoxidables austeníticos. Las mezclas con oxígeno que
se usarán en el sistema MIG como se verá a continuación, no deben
utilizarse con TIG debido al deterioro que ocasionan en el electrodo de
tungsteno. Las adiciones de nitrógeno no se recomiendan por la misma
razón.
Los metales de aporte más adecuados para la soldadura
TIG de los aceros inoxidables se indican en el apartado 4.3 de este
tutorial. Las varillas rectas se suelen utilizar en la soldadura TIG
manual, mientras que el material de aporte para los procesos
automatizados suelen suministrarse en forma de rollos o bobinas. Antes
de soldar el alambre desnudo deberá ser limpiado y almacenado en lugar
protegido y cubierto para evitar su contaminación con otros materiales.
- Recomendaciones operativas en el soldeo:
Al ser los electrodos en el proceso TIG elementos no
consumibles, se deben seleccionar aquellos electrodos que ofrezcan mucha
durabilidad y no se degraden (temperaturas de fusión > 4000 ºC) y a
la vez garanticen un correcto cebado y mantenimiento del arco.
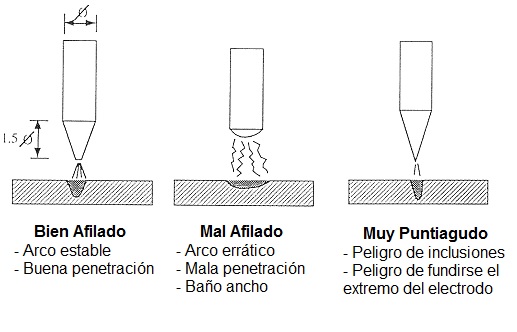
En este sentido, se recomienda elegir electrodos de
tungsteno aleados con torio (Th) o con circonio (Zr) que mejoren el
punto de fusión del tungsteno puro, y favorezcan el encendido y
estabilidad del arco.
Mantener el extremo del electrodo con un correcto
afilado es esencial para conseguir una soldadura de calidad y un arco
estable, según se muestra en la figura adjunta.
Como ya se dijo anteriormente, el establecimiento del
arco entre el electrodo y el metal base, se produce más fácilmente si se
cuenta con una fuente de alta frecuencia que permita iniciar la
soldadura y establecer el arco sin necesidad de tener que tocar con el
electrodo la pieza.
En ausencia de estos dispositivos, se puede iniciar el
arco frotando la superficie del metal base a soldar con el electrodo,
pero se corre el riesgo de contaminar al electrodo y también al metal
base. Para ello, puede resultar útil utilizar pequeños trozos de
planchuela de acero inoxidable adyacentes a la soldadura donde
establecer el arco, para eliminar así el posible daño en el metal de
base.
Del mismo modo, y con objeto de evitar la formación de
cráteres en el punto final del cordón, antes de levantar el electrodo y
apagar el arco, se deberá actuar sobre el pedal de la fuente para ir
disminuyendo de forma progresiva la intensidad de corriente. En caso de
no disponer de este dispositivo, se deberá aumentar la velocidad de
soldadura en los momentos finales de la soldadura antes de levantar el
electrodo, como ya se comentó anteriormente.
Realizar una buena práctica de apagado del arco es
especialmente importante en los cordones que constituyen las pasadas de
raíz, dado que éstos cordones sólo se realizan desde un lado, por lo que
las grietas que pudieran generarse serían difíciles de reparar.
Asimismo, se recomienda mantener la pistola TIG o
pinza porta-electrodos sobre el punto final de la soldadura unos
segundos para permitir que ésta solidifique y se enfríe bajo la
protección del chorro de salida del gas protector.
Cuando se vayan a ejecutar soldaduras que estén
sometidas a ambientes corrosivos severos, entonces se recomienda emplear
un metal de aporte de una aleación que sea de un grado más alto que la
composición del metal base, con objeto de dotar de resistencia a la
corrosión al cordón de soldadura.
Aunque es difícil saberlo, se estima que al menos el
50% del metal del cordón de soldadura en un procedimiento TIG proviene
del metal de aporte, por lo que se recomienda ser generoso en la
aplicación del metal de aportación para conseguir una aleación final que
esté enriquecida.
Sin embargo, es importante que la mezcla del metal
base con el metal de aporte se produzca antes que el cordón de soldadura
se solidifique, porque de lo contrario existirían zonas segregadas de
alta y baja aleación. Una causa de este tipo de segregación se debe a
una desigual fusión del metal de aporte, junto con una alta velocidad de
solidificación del cordón.
Tanto en el procedimiento MIG (Metal Inert Gas, cuando
se utiliza la protección gaseosa de un gas inerte) como también en el
MAG (Metal Active Gas, cuando se utiliza un gas activo), se establece un
arco eléctrico entre un electrodo consumible, que se presenta en forma
de un alambre desnudo, y la pieza a soldar o metal base.
Como se ha comentado, para la soldadura MIG, tanto el
arco como la soldadura se protegen del aire de la atmósfera mediante la
acción de una envolvente gaseosa, compuesta por gases inertes,
principalmente argón y/o helio.
Con el objeto de obtener una mejor acción del arco y
una mejor mojabilidad en la soldadura, en ocasiones se utilizan pequeñas
cantidades de gases activos, tales como dióxido de carbono, oxígeno e
hidrógeno.
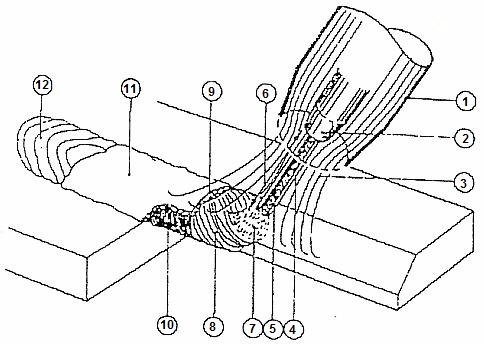
Leyenda de la figura adjunta:
1.-Boquilla; 2.-Tubo de contacto; 3.-Gas de
protección; 4.-Varilla (sólida o tubular); 5.-Flux en caso de varilla
tubular; 6.-Longitud libre de varilla (stik-out); 7.-Transferencia del
metal aportado; 8.-Baño de soldeo y escoria líquida; 9.-Escoria sólida
protegiendo al baño de fusión; 10.-Metal depositado; 11.-Escoria
solidificada; 12.-Metal de soldadura solidificado libre de escoria.
Entre las ventajas del proceso MIG sobre los demás procesos de soldadura, se pueden destacar las siguientes:
• Permite mayores velocidades de soldadura.
• Facilidad de automatizar el proceso, si se trata de grandes producciones.
• En general, es un procedimiento que ofrece una buena transferencia del metal de aporte a través del arco.
- Modos de transferencia del arco:
En la soldadura MIG, el modo de transferencia del
material de aporte al baño de fusión tiene una muy importante influencia
sobre las características del proceso.
Los tres modos más utilizados en la soldadura de
aceros inoxidables son por spray, corto circuito y arco pulsado. Para
obtener mayor información sobre los modos de transferencia de material
en la soldadura MIG, se invita al lector a consultar el Tutorial nº 53 "Fundamentos de la Soldadura MIG-MAG".
En la siguiente tabla se comparan las diferentes
aplicaciones de cada uno de los modos de transferencia en la soldadura
MIG de aceros inoxidables:
Tabla 5. Modos de transferencia en la soldadura MIG de aceros inoxidables.
|
|||
Spray
|
Corto circuito
|
Arco pulsado
|
|
Espesores
|
3 mm. mínimo
6 mm y más |
1,6 mm y más |
1,6 mm y más |
Posiciones
|
Plana y horizontal
|
Todas
|
Todas
|
Velocidad relativa de deposición
|
La más alta
|
La más alta
|
Intermedia
|
Diámetro típico del alambre
|
1,16 mm.
|
0,8 ó 0,9 mm.
|
0,9 ó 1,2 mm.
|
Corriente típica de soldadura
|
250-300 amperios
|
50-225 amperios
|
Arriba de picos de 250 amperios
|
Protección gaseosa
|
Argón-1%Oxígeno Argón-2%Oxígeno |
90%Helio- 7,5%Argón- 2,5%CO2 ó bien, 90%Argón- 7,5%Helio- 2,5%CO2 |
90%Helio- 7,5%Argón- 2,5%CO2 ó bien, 90%Argón- 7,5%Helio- 2,5%CO2 ó bien, Argón- 1%Oxígeno |
Cuando se emplea la soldadura MAG en aceros
inoxidables se recomienda la transferencia de material por spray de arco
que proporciona una penetración del cordón mucho más profunda que si se
emplease el procedimiento MAG por corto circuito.
- Equipamiento:
En caso de emplearse soldadura MIG, deberá utilizarse
corriente continua con polaridad inversa (electrodo conectado al ánodo o
polo positivo), con objeto de obtener una mayor penetración y arco más
estable. La corriente de polaridad directa se limita a aplicaciones que
requieren sólo una penetración superficial, tales como la soldadura en
solapa.
En general, las mismas fuentes de potencia, mecanismos
de alimentación de alambre y pistolas de soldadura que se usan para la
soldadura de aceros ordinarios, se pueden usar en los aceros
inoxidables. Para ampliar la información aquí expuesta, se vuelve a
recomendar la consulta del Tutorial nº 53 "Fundamentos de la Soldadura MIG-MAG".
En cualquier caso, el proceso MIG tiene más parámetros
que controlar que el TIG o la soldadura manual con electrodos
recubiertos, tales como amperaje, voltaje, pendiente de corriente,
alimentación de alambre, velocidad de pulsos y modo de transferencia del
arco.
Por lo tanto, las fuentes de potencia para la
soldadura MIG son, en general, más complejas y costosas. No obstante, en
la actualidad ya se fabrican nuevas fuentes para soldadura MIG, tales
como la de arco pulsado sinérgico, que han hecho la operación más
simple, ya que dispone de sólo un dial de control que debe manejar el
operador, y los otros parámetros se ajustarán automáticamente.
- Consumibles:
En cuanto a los gases de protección que se suelen
emplear con la soldadura MIG para aceros inoxidables está el argón,
helio o una mezcla de ambos. En ocasiones, para obtener mayor
estabilidad del arco y una mejor fluidez del baño de soldadura, se
utilizan adiciones de pequeñas cantidades de gases activos como dióxido
de carbono, oxígeno o hidrógeno.
Decir que para los procesos de soldadura MIG en aceros
inoxidables se recomienda la transferencia de material de aporte por
spray, para lo cual se deberá utilizar como gas protector Argón con 1 ó
2% de Oxígeno. Con ello se consiguen arcos estables y baños de fusión
muy calientes que deja un cordón de aspecto liso y con escasas
proyecciones.
Si se decide por el tipo de transferencia del metal de
aporte por cortocircuito y pulsado para soldaduras en posición,
entonces se recomienda emplear una mezcla de gases compuesto por un 90%
de Helio, 7,5% Argón y un 2,5% de CO2 que es una mezcla muy
popular en Norteamérica. No obstante en Europa el Helio es bastante
caro, y por ello se usa como alternativa una mezcla de 90% Argón, 7,5%
Helio y 2,5% CO2.
En todo caso, cualquiera que sea la combinación, el
gas de protección para la soldadura MIG deberá contener al menos un
97,5% de gases inertes (argón, helio o mezcla de los dos), mientras que
los gases activos presentes en la combinación, como el dióxido de
carbono (CO2) no deberá exceder del 2,5%, para que la calidad de la soldadura y la resistencia a la corrosión no se vean disminuidas.
Selección de electrodos
En la selección del contenido del material de aporte
que constituye el electrodo para la soldadura de los aceros inoxidables
es fundamental conocer el contenido de ferrita existente en el metal
base a soldar.
El comportamiento a la soldadura de los aceros
inoxidables austenítico, por ejemplo, varía según su estructura interna
que se trate, desde aquellos que son completamente austenítico como el
310, hasta otros que poseen doble estructura austenítica y ferrítica
como los grados 308, 309, 312, etc.
.
Al final, se recomienda que el porcentaje de ferrita
en el electrodo esté balanceado con el de austenita, para conseguir así
que el cordón de soldadura presente una adecuada resistencia al
agrietamiento, y a la vez también, una buena resistencia al impacto o a
la corrosión por tensiones, de acuerdo a las condiciones de servicio a
las que vaya a estar expuesta la pieza soldada.
En efecto, por un lado la presencia de ferrita reduce
la posibilidad de producirse fenómenos de agrietamiento en caliente del
cordón de soldadura, debido a que ciertos elementos e impurezas presente
en el acero, como el fósforo, azufre o silicio con bajo punto de
fusión, quedan atrapados durante el proceso de enfriamiento del cordón
de soldadura, siendo el germen de generación de futuras grietas internas
del cordón.
Resulta que estos elementos son mucho más solubles en
la ferrita que en la austenita, por lo que cierta cantidad de ferrita
ayudaría a absorber estas impurezas y evitar que quedasen atrapadas en
el cordón durante su enfriamiento, eliminando así la posibilidad de
generar grietas en el interior del cordón.
Por ello, en la mayoría de los materiales de aporte
para la soldadura de acero inoxidable austenítico contienen un
porcentaje de ferrita, que puede variar según el tipo de aplicación,
entre un 3% a un 20%.
Pero por otro lado, en ciertas ocasiones no es
recomendable la presencia de excesiva ferrita en el material de aporte,
por ejemplo, en aplicaciones criogénicas de muy bajas temperatura (-195
ºC), donde un incremento en el porcentaje de ferrita implicaría una
disminución de la resistencia al impacto del cordón, al ser la ferrita
muy frágil a estas temperaturas.
En otras aplicaciones, que impliquen ambientes
corrosivos pero en altas temperaturas, la ferrita puede producir también
una disminución importante de la resistencia a la oxidación, sobre todo
en los grados inoxidables al molibdeno como 316, 317 y sus versiones L de bajo carbono.
De todo lo anterior se deduce que para una correcta
selección del tipo de electrodo en las soldaduras de aceros inoxidables
es muy importante conocer el porcentaje de ferrita en su composición,
pues éste condicionará finalmente el contenido de ferrita que quede
presente en la soldadura.
Para medir el contenido de ferrita que quede presente
en el cordón de soldadura se puede conocer mediante el uso de
instrumentos de laboratorio sensibles al magnetismo (dado que la ferrita
es magnética y la austenita no), o bien se puede estimar por medio de
un examen metalográfico (método más exacto cuando la ferrita se
encuentra presente en un rango del 4 al 10%), o bien a través de
gráficos que pueden estimar con bastante exactitud el contenido de
ferrita a partir de la composición química del metal de aporte. Este
último método es el que va a ser desarrollado a continuación.
Con el uso del Diagrama de Schaeffler se podrá
determinar, entre otros datos, la estructura final del metal base, del
material de soldadura y del depósito soldado, y por ende las
características mecánicas del cordón de soldadura obtenido, para lo cual
será necesario conocer la composición química de los materiales en
cuestión.
Como se sabe, el cromo es un elemento alfágeno que
promueve la formación de la ferrita, mientras que el níquel
(austenítico) es gammágeno y se opone a dicha formación. Otros elementos
presentes en el acero actúan, aunque en distinta intensidad, como lo
hace el cromo o el níquel, es decir, que son alfágenos (formadores de
ferrita) o gammágenos (formadores de austenita).
Por ello, y para poder medir la importancia de uno u
otro grupo de elementos A. Schaeffler definió los conceptos de
Cromo-equivalente y Níquel-equivalente. El Cromo-equivalente incorpora
los elementos formadores de ferrita y el Níquel-equivalente los
formadores de austenita.
Los elementos presentes en cada grupo irán
multiplicado por un factor que dependerá de su grado de influencia en la
formación de ferrita o austenita, según el caso.
• Níquel-equivalente = %Ni + 0,5% Mn + 30%C
• Cromo-equivalente = %Cr + %Mo + 1,5%Si + 0,5%Nb + 2%Ti
Con el empleo del diagrama de Schaeffler se podrá
determinar las características mecánica del cordón de soldadura obtenido
cuando se unan dos piezas de acero inoxidable.
Dichas características dependerán del punto del
diagrama donde se ubique el metal depositado, que será el resultante de
una mezcla del metal de aporte procedente del electrodo empleado y los
materiales base de las piezas que se pretenden soldar.
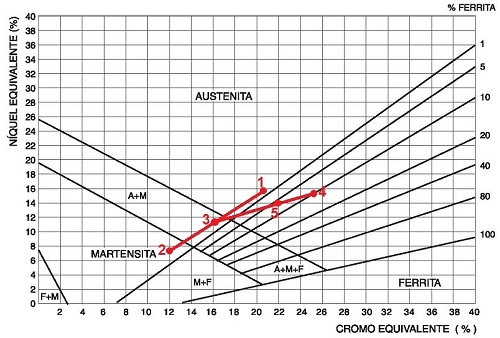
Las piezas del metal base podrán ser disímiles, es
decir, piezas de aceros inoxidables de familias distintas, por ejemplo,
una pieza de acero inoxidable austenítico que se pretenda soldar con
otra pieza de inoxidable martensítico.
En la figura adjunta se representa una aplicación
práctica del diagrama de Schaeffler, donde los puntos 1 y 2 en color
rojo sobre el diagrama representan la composición química de las dos
piezas de metal base que se pretenden soldar (en este caso, el metal
base 1 es una pieza de acero inoxidable austenítico y el metal base 2 un
acero inoxidable martensítico).
Como se sabe, durante la ejecución de la soldadura el
foco de calor que genera el baño de fusión, fundirá también parte del
metal base de ambas piezas, las cuales se van a mezclar.
Si por las condiciones de preparación de bordes
permiten que ambos materiales participen en similar proporción (piezas
de igual espesor, con igual bisel, igual precalentamiento de ambas
piezas, arco simétricamente direccionado...) el punto en el diagrama que
representa la mezcla de ambas piezas de metal base se situará en un
punto intermedio de la recta que une los puntos 1 y 2 (punto 3).
Por otro lado, haciendo uso de las expresiones
anteriores se determina el valor de Cromo-equivalente y
Níquel-equivalente del metal de aporte. En el diagrama dicho metal de
aportación quedará representado con el punto 4.
El punto final que representa la mezcla final
resultante del cordón de soldadura (mezcla de los metales bases y del
metal de aporte) se situará en un punto de la recta que une el punto 3
con el punto 4.
Este punto final (punto 5 en el diagrama adjunto), que
se situará en la recta que une los puntos 3 y 4, estará más o menos
cerca de uno u otro extremo en función del porcentaje de dilución del
metal base (que a su vez dependerá del proceso de soldadura empleado, de
la intensidad de corriente, de la longitud del arco, etc.).
En un proceso típico de soldadura por arco manual con
electrodo metálico revestido (SMAW) el porcentaje de dilución del metal
base se sitúa en torno al 30% (es decir, el 30% del baño de fusión
corresponde al metal base, siendo el resto metal de aporte fundido). Y
en este caso, el punto final del cordón de soldadura (punto 5) se
situará más próximo al punto 4.
Conocer la posición del
punto 5 en la gráfica es muy importante porque dará idea de las
características y composición final del cordón de soldadura que se ha
obtenido.
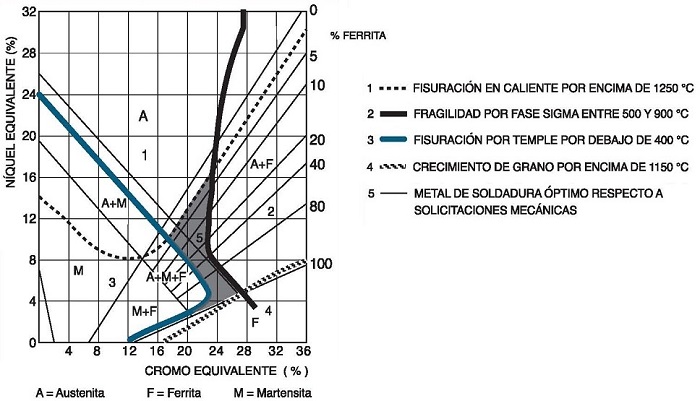
Sobre un diagrama de Schaeffler de la figura de
arriba, donde se muestran las fases austeníticas, ferríticas y
martensíticas, se han señalado también aquellos límites que se
recomienda no sobrepasar para obtener un cordón de soldadura lo más
óptimo posible.
Así, se representa el límite que indica las zonas de
fragilización en frío debido a la presencia de martensita, el límite que
marca la zona de fragilidad en caliente originada por la presencia de
austenita, o la zona de fragilidad originada por la presencia de fase
sigma y la zona de crecimiento de grano ferrítico.
En dicha figura adjunta también se sombrea de gris la
zona más propicia para situar la composición final de la mezcla del
cordón de soldadura.
Como criterio general, se recomienda en todo caso
posicionarse en la zona austenítica que contenga además un porcentaje de
entre el 5 y el 10% de ferrita.
A continuación se relacionan los tipos de electrodos
más empleados para la soldadura de aceros inoxidables, indicando una
breve descripción del mismo donde se indique sus principales
aplicaciones y las clases de aceros inoxidables para los que son
empleados, las posiciones de soldeo recomendadas para cada electrodo,
tipo de corriente a emplear en la soldadura, composición química del
electrodo y propiedades mecánicas que aporta al metal de soldadura.
Electrodo, AWS: E 308/308H-16
|
|
![]() |
Procedimiento: Soldadura por Arco Manual.
|
Descripción: Electrodo
de composición típica 19%Cr y 10%Ni. Altamente resistente contra la
fragilidad por fase sigma. Fácil remoción de escoria y excelente
presentación del cordón.
|
|
Usos: En
general se recomienda para soldadura de metales base de composición
similar. Para soldadura de aceros inoxidables que contienen 16-21%Cr,
8-13%Ni, y con altos contenidos de carbono, tipo 304H. Se utiliza en los
casos donde el acero inoxidable está sometido a temperaturas de
servicios inferiores a 750º C.
|
|
Aplicaciones típicas: Para la soldadura de aceros tipo AISI 301, 302, 304 y 305.
|
|
Posiciones de soldadura: Plana, Horizontal, Vertical, Sobrecabeza.
|
|
Tipo de corriente: Corriente Continua Polaridad Inversa (CCPI), Corriente Alterna (CA)
|
|
Composición química:
C: 0,05% Mn: 0,54% Si: 0,67% P: 0,021% S: 0,005% Cr: 18,7% Ni: 10,2% Mo: 0,07% |
|
Propiedades mecánicas:
Resistencia a la tracción: 590 MPa Elongación (L=4d): 53% |
Electrodo, AWS: E 308 L-16
|
|
![]() |
Procedimiento: Soldadura por Arco Manual.
|
Descripción: Este
tipo de electrodo tiene un revestimiento rutílico, lo que permite
soldar con CA o CCPI. Proporciona un arco estable de transferencia
spray, depósito de excelente forma y apariencia. La escoria se desprende
fácilmente, con muy buena reanudación de arco. El depósito es de acero
inoxidable austenítico.
|
|
Usos: Aceros
inoxidables austenítico con un contenido extra bajo de carbono. El
contenido de 0,04% de carbono evita la formación y la precipitación de
carburos. Ofrece una excelente protección contra la corrosión
intergranular. Se recomienda especialmente para aplicaciones resistentes
a la corrosión, producida por los ácidos y soluciones de celulosa.
También se recomienda su uso en soldaduras intermitentes.
|
|
Aplicaciones típicas: Para
la soldadura de aceros inoxidables grados 304, 304L, 308, 308L, 321,
347, 348. Para la soldadura de equipos químicos y petroquímicos.
Estanques.
|
|
Posiciones de soldadura: Plana, Horizontal, Vertical, Sobrecabeza.
|
|
Tipo de corriente: Corriente Continua Polaridad Inversa (CCPI), Corriente Alterna (CA).
|
|
Composición química:
C: 0,02% Mn: 0,63% Si: 0,76% P: 0,025% S: 0,008% Cr: 18,7% Ni: 10,0% Mo: 0,18% |
|
Propiedades mecánicas:
Resistencia a la tracción: 590 MPa Elongación (L=4d): 53% |
Electrodo, AWS: E 309 L-16
|
|
![]() |
Procedimiento: Soldadura por Arco Manual.
|
Descripción: Su
bajo contenido de carbono previene la precipitación de carburos de
cromo. Excelente contra la corrosión intergranular. Excelente
operatividad en toda posición.
|
|
Usos: Adecuado
para uniones de aceros inoxidables, así como para aceros bajo en
carbono y de baja aleación. Apto para "buttering" y como depósito base
para aplicaciones que requieren un posterior recubrimiento duro. Su
depósito tiene excelente resistencia a la corrosión a temperatura
ambiente, aunque su uso principal es para resistir la oxidación a altas
temperaturas (1000ºC).
|
|
Aplicaciones típicas: Adecuado para aceros AISI 309,309L, 309Cb, 304, 304L, 321, 347 y soldaduras disímiles.
|
|
Posiciones de soldadura: Plana, Horizontal, Vertical, Sobrecabeza.
|
|
Tipo de corriente: Corriente Continua Polaridad Inversa (CCPI), Corriente Alterna (CA).
|
|
Composición química:
C: 0,02% Mn: 0,69% Si: 0,80% P: 0,022% S: 0,009% Cr: 22,5% Ni: 13,4% Mo: 0,16% |
|
Propiedades mecánicas:
Resistencia a la tracción: 555 MPa Elongación (L=4d): 42% |
Electrodo, AWS: E 309 MoL-16
|
|
![]() |
Procedimiento: Soldadura por Arco Manual.
|
Descripción: Electrodo
con revestimiento rutílico, para uso en aceros inoxidables
austeníticos. Su composición es igual al E-309Mo, excepto por el
contenido de carbono reducido, el cual disminuye la posibilidad de
sufrir corrosión intergranular y corrosión por pitting.
|
|
Usos: Ideal
para uniones disímiles entre aceros inoxidables y aceros al carbono de
baja aleación. También se usa para soldadura de aceros inoxidables que
contienen Cr-Ni-Mo.
|
|
Aplicaciones típicas: Soldadura
de metales disímiles, y para la soldadura de aceros AISI 309 MoL y para
reparaciones de Clad Steel tipo AISI 316 y 316L.
|
|
Posiciones de soldadura: Plana, Horizontal, Vertical, Sobrecabeza.
|
|
Tipo de corriente: Corriente Continua Polaridad Inversa (CCPI), Corriente Alterna (CA).
|
|
Composición química:
C: 0,02% Mn: 0,73% Si: 0,51% P: 0,018% S: 0,010% Cr: 22,3% Ni: 12,5% Mo: 2,39% |
|
Propiedades mecánicas:
Resistencia a la tracción: 680 MPa Elongación (L=4d): 40% |
Electrodo, AWS: E 316 / 316H 16
|
|
![]() |
Procedimiento: Soldadura por Arco Manual.
|
Descripción: Electrodo
rutílico para aceros austeníticos de composición 19%Cr, 12%Ni y 2,5%Mo.
El electrodo E 316H es igual al E 316 excepto que en el primer caso el
contenido de carbono ha sido restringido al rango superior aceptado por
el 316, esto es: entre 0,04% y el 0,08% de C. De esta manera se consigue
proporcionar mayor resistencia a la tracción y al creep a altas
temperaturas.
|
|
Usos: Apto
para soldadura de aceros inoxidables que contienen 16-21%Cr, 10-15%Ni y
0-3%Mo, con alto contenido de carbono. Aceros tipo 316 y aleaciones
similares. Son utilizados también para aplicaciones sometidas a altas
temperaturas de servicio (hasta 750º C aproximadamente).
|
|
Aplicaciones típicas: Para la soldadura de equipos químicos y petroquímicos, industria lechera, etc.
|
|
Posiciones de soldadura: Plana, Horizontal, Vertical, Sobrecabeza.
|
|
Tipo de corriente: Corriente Continua Polaridad Inversa (CCPI), Corriente Alterna (CA).
|
|
Composición química:
C: 0,05% Mn: 1,20% Si: 0,80% P: 0,020% S: 0,020% Cr: 18,7% Ni: 12,0% Mo: 2,3% |
|
Propiedades mecánicas:
Resistencia a la tracción: 600 MPa Elongación (L=4d): 35% |
Electrodo, AWS: E 316 L-16
|
|
![]() |
Procedimiento: Soldadura por Arco Manual.
|
Descripción: Genera
un arco suave y estable de transferencia spray. Depósito de excelente
apariencia que se ajusta con facilidad a las exigencias del trabajo. La
escoria se desprende fácilmente y como el arco es rápidamente
restablecido, se usa en soldadura intermitente.
|
|
Usos: El
electrodo E 316L ha sido diseñado para aceros austeníticos con un
contenido extra-bajo de carbono. El contenido máximo de 0,04% de carbono
evita la formación y precipitación de carburos. Ofrece una excelente
protección contra la corrosión intergranular. Se recomienda
especialmente para aplicaciones resistentes a la corrosión, cuando
existen posibilidades de "picadura" (ataque por ácido). No es necesario
tratamiento térmico posterior.
|
|
Aplicaciones típicas: Para la soldadura de aceros 316, 316L, 317, 317L, 316Ti y 318.
|
|
Posiciones de soldadura: Plana, Horizontal, Vertical, Sobrecabeza.
|
|
Tipo de corriente: Corriente Continua Polaridad Inversa (CCPI), Corriente Alterna (CA).
|
|
Composición química:
C: 0,02% Mn: 0,63% Si: 0,77% P: 0,022% S: 0,009% Cr: 18,5% Ni: 11,7% Mo: 2,7% |
|
Propiedades mecánicas:
Resistencia a la tracción: 580 MPa Elongación (L=4d): 48% |
Electrodo, AWS: E 347-16
|
|
![]() |
Procedimiento: Soldadura por Arco Manual.
|
Descripción: Electrodo
que tiene revestimiento rutílico, lo que permitesoldar con CA o CC con
electrodo positivo (polaridad inversa). El arco con una transferencia de
tipo spray resulta muy estable. Genera un depósito que fluye para
producir soldaduras de forma y apariencia excelentes, que se ajusta para
permitir un buen control en soldadura fuera de posición. La escoria se
desprende fácilmente.
|
|
Usos: Este
tipo de electrodo ha sido diseñado para aceros tipo 347 y 321. Sin
embargo, también puede ser usado para soldar cualquier tipo de
inoxidable donde se requiera una máxima resistencia a la corrosión. El
niobio que contiene inhibe la precipitación de carburos, disminuyendo
notablemente la corrosión.
|
|
Aplicaciones típicas: Aceros 347, 321, 304 y 308L. También para la soldadura de componentes para ácidos, gases y agua.
|
|
Posiciones de soldadura: Plana, Horizontal, Vertical, Sobrecabeza.
|
|
Tipo de corriente: Corriente Continua Polaridad Inversa (CCPI), Corriente Alterna (CA).
|
|
Composición química:
C: 0,03% Mn: 0,76% Si: 0,90% P: 0,032% S: 0,005% Cr: 18,5% Ni: 10,0% Mo: 0,25% Nb: 0,40% |
|
Propiedades mecánicas:
Resistencia a la tracción: 650 MPa Elongación (L=4d): 39% |
Electrodo, AWS: E 410NiMo-1
|
|
![]() |
Procedimiento: Soldadura por Arco Manual.
|
Descripción: Electrodo
similar al E410 salvo que contiene menos cromo y más níquel. El
objetivo es eliminar la ferrita, debido a los efectos mecánicos
perjudiciales generados por esta fase. Proporciona mejor resistencia al
agrietamiento que el E410 para la unión de metales base de este mismo
tipo. Además es un electrodo de bajo contenido en hidrógeno, por lo cual
se recomienda seguir todos los pasos que corresponden tanto a lo que se
refiere al presecado como al mantenimiento de un electrodo de bajo
hidrógeno. El tratamiento térmico post-soldadura no deberá exceder los
620ºC.
|
|
Usos: Para
la soldadura de aceros 403, 405, 410, 410S, 414, 416, 420 y ASTM CAGNA.
Muy apropiado para ruedas de turbinas tipo Pelton, Francis, Kaplan.
|
|
Aplicaciones típicas: Reconstrucción de válvulas y fittings. Aceros martensíticos, inoxidables al cromo, fundidos al Cr Ni.
|
|
Posiciones de soldadura: Plana, Horizontal, Vertical, Sobrecabeza.
|
|
Tipo de corriente: Corriente Continua Polaridad Inversa (CCPI).
|
|
Composición química:
C: 0,04% Mn: 0,48% Si: 0,29% P: 0,019% S: 0,011% Cr: 11,5% Ni: 4,1% Mo: 0,48% |
|
Propiedades mecánicas:
Tratamiento térmico: 610 ºC (durante una hora) Resistencia a la tracción: 827 MPa Elongación (L=4d): 17% |
Electrodo, AWS: E 2209-16
|
|
![]() |
Procedimiento: Soldadura por Arco Manual.
|
Descripción: Este
tipo de electrodo tiene una estructura dúplex consistente en una matriz
austenítica-ferrítica. El metal depositado combina una alta resistencia
a la tracción con propiedades mejoradas de resistencia a la corrosión
bajo tensión y por picadura. Transferencia tipo spray con baja
salpicadura. Fácil inicio de arco reduciendo las posibilidades de
defectos asociados al proceso inicial del establecimiento del arco.
Excelente resistencia a la humedad.
|
|
Usos: Empleado para la soldadura de aceros inoxidables dúplex con un contenido aproximado del 22% de cromo.
|
|
Aplicaciones típicas: El
material depositado es resistente a la corrosión intergranular y por
pitting. Presenta ventajas en soldadurade aceros inoxidables del tipo
austeno-ferrítico como el 18Cr/8Ni/Mo (3RE60) 22Cr/5Ni/3Mo (2205) y
23Cr/4Ni (2304). Posee buena resistencia a la corrosión bajo tensión,
especialmente en ambientes que contienen H2S.
|
|
Posiciones de soldadura: Plana, Horizontal, Vertical, Sobrecabeza.
|
|
Tipo de corriente: Corriente Continua Polaridad Inversa (CCPI), Corriente Alterna (CA).
|
|
Composición química:
C: 0,03% Mn: 1,01% Si: 0,38% P: 0,011% S: 0,013% Cr: 22,9% Ni: 10,10% Mo: 3,00% |
|
Propiedades mecánicas:
Resistencia a la tracción: 794 MPa Elongación (L=4d): 27% |
Electrodo, AWS: ER 308L
|
|
![]() |
Procedimiento: Soldadura MIG y TIG.
|
Descripción: Este
tipo de electrodo está diseñado para los procesos de soldadura con gas
inerte (MIG y TIG). Tiene un análisis químico bien equilibrado, un
contenido extra-bajo de carbono que minimiza la precipitación de
carburos. Propiedades mecánicas bien balanceadas. Arco estable de
transferencia spray, en el caso de usar como protección gaseosa
indurming inoxidable o argón.
|
|
Usos: El
alambre 308L es similar al 308, excepto por su contenido extra-bajo en
carbono (menor al 0,03%). Es utilizado para soldar aceros AISI tipos
304L y 308L que pueden ser utilizados en un amplio rango de condiciones
corrosivas, sin necesidad de hacer tratamientos térmicos posteriores a
la soldadura.
|
|
Aplicaciones típicas: Para
la soldadura de aceros 308L, 304L, 308, 321 y 347. Equipos y estanques
de proceso y almacenamiento de productos alimenticios y químicos. Bombas
e intercambiadores de calor.
|
|
Posiciones de soldadura: Plana, Horizontal, Vertical, Sobrecabeza.
|
|
Tipo de corriente: Corriente Continua Polaridad Inversa (CCPI).
|
|
Composición química:
C: 0,02% Mn: 1,90% Si: 0,38% P: 0,02% S: 0,01% Cr: 19,8% Ni: 9,8% Mo: 0,19% |
|
Propiedades mecánicas:
Resistencia a la tracción: 570 MPa Elongación (L=4d): 44% |
Electrodo, AWS: ER 309L
|
|
![]() |
Procedimiento: Soldadura MIG y TIG.
|
Descripción: Electrodo
válido para procesos de soldadura con gas inerte (MIG y TIG).
Proporciona un arco estable de transferencia spray con indurming inox. o
argón. Su bajo porcentaje de carbono reduce la precipitación de
carburos incrementando la resistencia a la corrosión intergranular.
|
|
Usos: El
alambre 309L es similar al 309, excepto por su contenido extra bajo de
carbono (menos del 0,03%). Es utilizado para soldar aceros AISI tipo
309L que pueden ser utilizados en un amplio rango de condiciones
corrosivas, y sin necesidad de hacer tratamientos térmicos posteriores a
la soldadura.
|
|
Aplicaciones típicas: Para
la soldadura de aceros 309L, 304L, 309, 321 y 347. Soldadura de equipos
de procesos y almacenamiento de productos alimenticios y químicos
corrosivos.
|
|
Posiciones de soldadura: Plana, Horizontal, Vertical, Sobrecabeza.
|
|
Tipo de corriente: Corriente Continua Polaridad Inversa (CCPI).
|
|
Composición química:
C: 0,01% Mn: 1,60% Si: 0,42% P: 0,021% S: 0,002% Cr: 23,0% Ni: 13,7% Mo: 0,05% |
|
Propiedades mecánicas:
Resistencia a la tracción: 570 MPa Elongación (L=4d): 42% Energía absorbida: 100 J a 0 ºC |
Electrodo, AWS: ER 316L
|
|
![]() |
Procedimiento: Soldadura MIG y TIG.
|
Descripción: Tipo
de electrodo diseñado para procesos de soldadura con gas inerte (MIG y
TIG). Posee una composición química bien equilibrada, y proporciona un
metal de aporte depositado bastante uniforme y con propiedades mecánicas
bien balanceadas. Arco estable de transferencia spray con gases
indurming inox. o argón.
|
|
Usos: Válido
para aceros tipo 316L, 316, 318 y aleaciones similares con contenido
extra bajo de carbono. El contenido del 0,04% de carbono máximo en el
metal depositado evita la formación y precipitación de carburos. Ofrece
una excelente protección contra la corrosión intergranular. Para
aplicaciones resistentes a la corrosión cuando hay posibilidades de
"picadura" (ataque por ácido). No es necesario tratamiento térmico
posterior.
|
|
Aplicaciones típicas: Para
la soldadura de aceros 316, 316L y 318. Equipos químicos y
petroquímicos. Industria alimenticia, de papel, turbinas y bombas, etc.
Intercambiadores de calor.
|
|
Posiciones de soldadura: Plana, Horizontal, Vertical, Sobrecabeza.
|
|
Tipo de corriente: Corriente Continua Polaridad Inversa (CCPI).
|
|
Composición química:
C: 0,02% Mn: 1,69% Si: 0,38% P: 0,030% S: 0,008% Cr: 18,1% Ni: 11,1% Mo: 2,1% |
|
Propiedades mecánicas:
Resistencia a la tracción: 570 MPa Elongación (L=4d): 40% Energía absorbida: 90 J a 0 ºC |
Electrodo, AWS: E 308LT1-1/ E308LT1-4
|
|
![]() |
Procedimiento: Soldadura Tubular.
|
Descripción: Alambre
tubular con protección gaseosa externa. Gas de protección Indurming 20 ó
100% CO2. Presenta una excelente soldabilidad y mejorada resistencia al
creep a alta temperatura. El metal depositado contiene un óptimo
contenido de ferrita en su estructura austenítica, ofreciendo así una
soldabilidad excelente con baja susceptibilidad al agrietamiento.
|
|
Usos: Diseñado para soldadura MIG de aceros inoxidables tipo 18%Cr-8%Ni de bajo contenido de carbono.
|
|
Aplicaciones típicas: Para la soldadura de aceros inoxidables AISI 304, 304L, 304LN, ASTM A 157 Gr. C9, A320 Gr. B8C ó D.
|
|
Posiciones de soldadura: Plana, Horizontal, Vertical, Sobrecabeza.
|
|
Tipo de corriente: Corriente Continua Polaridad Inversa (CCPI).
|
|
Composición química:
C: 0,03% Mn: 1,90% Si: 0,79% Cr: 19,8% Ni: 10,2% Fe: balance |
|
Propiedades mecánicas:
Resistencia a la tracción: 610 MPa Elongación (L=4d): 35% |
Electrodo, AWS: E 309LT1-1/-4
|
|
![]() |
Procedimiento: Soldadura Tubular.
|
Descripción: El
metal depositado contiene bastante ferrita a su estructura austenítica,
ofreciendo así una mejor soldabilidad junto con una elevada resistencia
a la temperatura y a la corrosión. Es fácil de operar con poderosa
penetración, transferencia tipo spray, mínima salpicadura y escoria auto
desprendente.
|
|
Usos: Fue
diseñado para soldadura MIG de aceros inoxidables tipo 18%Cr - 8%Ni de
bajo contenido de carbono. Soldadura de uniones disímiles y entre aceros
de alta resistencia, soldadura de aceros al carbono y aceros de baja
aleación templables y revenidos, aceros ferríticos al Cr y austeníticos
al Cr- Ni y aceros al manganeso. Además este electrodo se usa para
generar una primera capa resistente a la corrosión en soldaduras de
aceros ferríticos-perlíticos en partes de tanques a presión y calderas.
|
|
Aplicaciones típicas: Para la soldadura de aceros inoxidables 309 y 309Cb, aceros disímiles y aceros al 12% Ni.
|
|
Posiciones de soldadura: Plana, Horizontal, Vertical, Sobrecabeza.
|
|
Tipo de corriente: Corriente Continua Polaridad Inversa (CCPI).
|
|
Composición química:
C: 0,03% Mn: 1,92% Si: 0,80% Cr: 23,8% Ni: 13,3% Fe: balance |
|
Propiedades mecánicas:
Resistencia a la tracción: 600 MPa Elongación (L=4d): 38% |
Electrodo, AWS: E316LT1-1/-4
|
|
![]() |
Procedimiento: Soldadura Tubular.
|
Descripción: Electrodo de alambre tubular con protección gaseosa externa para soldadura de aceros inoxidables. Gas de protección: 100% CO2
o Indurming 20. Produce una escoria que se auto desprende, y una
transferencia tipo spray. Es de excelente soldabilidad y elevada
resistencia al creep y altas temperaturas. El metal de soldadura
contiene óptimo contenido de ferrita en su estructura austenítica, que
le confiere su buena soldabilidad con baja tendencia al agrietamiento.
|
|
Usos: Electrodo
diseñado para soldadura MIG de acero inoxidable del tipo 18%Cr - 12%Ni -
2%Mo y de bajo carbono. Su bajo contenido de carbono le da buena
resistencia para la mayoría de los tipos de corrosión del metal de
soldadura.
|
|
Aplicaciones típicas: Para la soldadura de aceros AISI 316L, 316Ti, 316Cb.
|
|
Posiciones de soldadura: Plana, Horizontal, Vertical, Sobrecabeza.
|
|
Tipo de corriente: Corriente Continua Polaridad Inversa (CCPI).
|
|
Composición química:
C: 0,03% Mn: 1,85% Si: 0,75% Cr: 18,7% Ni: 11,4% Mo: 2,5% Fe: balance |
|
Propiedades mecánicas:
Resistencia a la tracción: 620 MPa Elongación (L=4d): 38% |
Electrodo, AWS: E308LTO-3
|
|
![]() |
Procedimiento: Soldadura Tubular.
|
Descripción: Electrodo
de alambre tubular auto protegido para la soldadura de acero
inoxidable. La composición del metal depositado es la misma que la del
electrodo E308LTO-3 excepto por el contenido de carbono. Su bajo
contenido de carbono le permite obtener resistencia a la corrosión
intergranular por precipitación de carburos, sin necesidad de hacer uso
de elementos estabilizadores tales como culombio y titanio.
|
|
Usos: Base
de recubrimientos duros y rellenos de polines. Su metal depositado no
es tan resistente a elevadas temperaturas como el depósito obtenido con
E-308 estabilizado con culombio y titanio.
|
|
Aplicaciones típicas: Su depósito Cr-Ni permite soldar aceros inoxidables de grados 302, 303, 304, 305, 308.
|
|
Posiciones de soldadura: Plana, Horizontal.
|
|
Tipo de corriente: Corriente Continua Polaridad Inversa (CCPI).
|
|
Composición química:
C: 0,03% Mn: 0,5-2,5% Si: 1,0% Cr: 19,5-21% Ni: 9,0-11,0% Fe: balance |
|
Propiedades mecánicas:
Resistencia a la tracción: 520 MPa Elongación (L=4d): 35% |
Electrodo, AWS: ER308/308H-16
|
|
![]() |
Procedimiento: Soldadura TIG.
|
Descripción: Varilla
para soldar aceros inoxidables con proceso TIG. Composición nominal
19%-Cromo y 9%-Níquel. La composición química de la varilla ER-308H es
la misma que la varilla ER-308 excepto que el contenido en carbono ha
sido restringido al rango superior del aceptado para la varilla ER-308.
Un contenido de carbono de 0,04 a 0,08% proporciona más alta
resistencia.
|
|
Usos: Este
tipo de varilla es usada frecuentemente para soldar metales base de
composiciones similares. Apropiada para temperatura de servicio de hasta
750°C.
|
|
Aplicaciones típicas: Para la soldadura de aceros base tipo 304H, 308H y sus derivados.
|
|
Posiciones de soldadura: Plana, Horizontal, Vertical, Sobrecabeza.
|
|
Tipo de corriente: Corriente Continua Polaridad Inversa (CCPI).
|
|
Composición química:
C: 0,05% Mn: 1,85% Si: 0,44% P: 0,02% S: 0,001% Cr: 19,90% Ni: 9,29% Mo: 0,09% |
|
Electrodo, AWS: ER308 L
|
|
![]() |
Procedimiento: Soldadura TIG.
|
Descripción: Varilla
con bajo contenido en carbono para soldar acero inoxidable con proceso
TIG. El bajo contenido de carbono en el metal de aporte (0,03 máximo)
contribuye a disminuir la posibilidad de precipitación de carburos,
incrementando la resistencia a la corrosión intergranular sin necesidad
de hacer uso de estabilizadores, tales como el culombio o titanio.
|
|
Usos: Adecuada
para uso de aceros inoxidables que contienen 16-21%Cr, 8-13%Ni, aceros
estabilizados y no estabilizados (302, 304, 304L, 304LN, 308, 321, 347).
|
|
Aplicaciones típicas: Para
la soldadura en equipos de proceso y almacenamiento de productos
alimenticios y químicos. Bombas, intercambiadores de calor.
|
|
Posiciones de soldadura: Plana, Horizontal, Vertical, Sobrecabeza.
|
|
Tipo de corriente: Corriente Continua Polaridad Directa (CCPD).
|
|
Composición química:
C: 0,02% Mn: 1,90% Si: 0,38% P: 0,02% S: 0,01% Cr: 19,80% Ni: 9,80% Mo: 0,19% |
|
Electrodo, AWS: ER 309L
|
|
![]() |
Procedimiento: Soldadura TIG.
|
Descripción: Varilla
con bajo contenido de carbono para proceso TIG. Este electrodo está
diseñado para cumplir con los requisitos de los aceros inoxidables que
utilizan procesos de soldadura con gas inerte. El bajo porcentaje de
carbono en el metal depositado reduce la posibilidad de precipitación de
carburos, incrementando así la resistencia a la corrosión
intergranular.
|
|
Usos: Es
utilizado para soldar aceros inoxidables AISI tipos 304L y 309L, que
pueden ser utilizados en un amplio rango de condiciones corrosivas.
|
|
Aplicaciones típicas: Para
la soldadura de aceros inoxidables 309L, 304L, 309, 321 y 347.
Soldadura de equipos de proceso y almacenamiento de productos
alimenticios y químicos corrosivos.
|
|
Posiciones de soldadura: Plana, Horizontal, Vertical, Sobrecabeza.
|
|
Tipo de corriente: Corriente Continua Polaridad Directa (CCPD).
|
|
Composición química:
C: 0,01% Mn: 1,60% Si: 0,42% P: 0,021% S: 0,002% Cr: 23,0% Ni: 13,7% Mo: 0,05% |
|
Electrodo, AWS: ER 316 H
|
|
![]() |
Procedimiento: Soldadura TIG.
|
Descripción: Varilla
TIG para soldar aceros inoxidables. La composición química del metal de
aporte es la misma que la varilla ER-316, excepto que el contenido de
carbono ha sido restringido al rango superior aceptado por la varilla
ER-316. El contenido de carbono se sitúa entre 0,04 a 0,08%, lo que
proporciona más alta resistencia.
|
|
Usos: Apta para temperaturas de servicio hasta 750°C.
|
|
Aplicaciones típicas: Para la soldadura de metales base tipo 316H.
|
|
Posiciones de soldadura: Plana, Horizontal, Vertical, Sobrecabeza.
|
|
Tipo de corriente: Corriente Continua Polaridad Directa (CCPD).
|
|
Composición química:
C: 0,05% Mn: 1,64% Si: 0,45% P: 0,020% S: 0,003% Cr: 19,11% Ni: 12,70% Mo: 2,30% |
|
Electrodo, AWS: ER 316 L
|
|
![]() |
Procedimiento: Soldadura TIG.
|
Descripción: Varilla
con un bajo contenido de carbono para proceso TIG. Formulada para
cumplir con los requisitos de los aceros inoxidables que utilizan
procesos de soldadura con gas inerte. El bajo porcentaje de carbono en
el metal depositado reduce la posibilidad de precipitación de carburos,
incrementando así la resistencia a la corrosión intergranular.
|
|
Usos: Uso
en industria alimenticia, de papel, componentes de turbinas, bombas. Se
recomienda para aplicaciones resistentes a la corrosión cuando hay
posibilidades de "picadura" (ataque por ácido).
|
|
Aplicaciones típicas: Para
la soldadura de aceros inoxidables que contienen 16-21%Cr, 10-15%Ni,
0-3%Mo, aceros estabilizados y no estabilizados tipos 316, 316L, 317,
317L, 316Ti, 318.
|
|
Posiciones de soldadura: Plana, Horizontal, Vertical, Sobrecabeza.
|
|
Tipo de corriente: Corriente Continua Polaridad Directa (CCPD).
|
|
Composición química:
C: 0,02% Mn: 1,69% Si: 0,38% P: 0,030% S: 0,008% Cr: 18,1% Ni: 11,1% Mo: 2,1% |
|
Electrodo, AWS: ER 2209
|
|
![]() |
Procedimiento: Soldadura TIG.
|
Descripción: Varilla
TIG con estructura dúplex, la cual lo hace altamente resistente a la
corrosión bajo tensión en ambientes con presencia de cloruros. El alto
contenido de cromo y molibdeno proporciona excelente resistencia a la
corrosión por pitting.
|
|
Usos: Debido
al balance existente entre las fases austeníticas y ferríticas,
presentan ventajas en severas condiciones de cloruros. Combinan algunas
de las mejores características de los aceros inoxidables austeníticos y
ferríticos. Mientras la austenita proporciona ductilidad, la ferrita
proporciona resistencia a la corrosión bajo tensión.
|
|
Aplicaciones típicas: :
Para la soldadura de aceros inoxidables del tipo austeno-ferrítico como
el 18Cr/8Ni/Mo (3RE60), 22Cr/5Ni/3Mo (2205) 23Cr/4Ni (2304).
|
|
Posiciones de soldadura: Plana, Horizontal, Vertical, Sobrecabeza.
|
|
Tipo de corriente: Corriente Continua Polaridad Directa (CCPD).
|
|
Composición química:
C: 0,02% Mn: 1,33% Si: 0,46% P: 0,020% S: 0,01% Cr: 23,32% Ni: 8,15% Mo: 3,15% N: 0,15% |
|
No hay comentarios:
Publicar un comentario