Conformado plástico son todos aquellos procesos que se busca generar forma a metales, de tal manera que su volumen y masa se conserven, desplazándose las partículas de una posición a otra.
Importancia: Se utiliza para elaborar múltiples artículos en diferentes formas y fabricado en serie, haciendo que su demanda se incremente dependiendo de sus características mecánicas que posee el material al igual que su gran maleabilidad y ductibilidad.
Clasificación del Proceso de Conformado
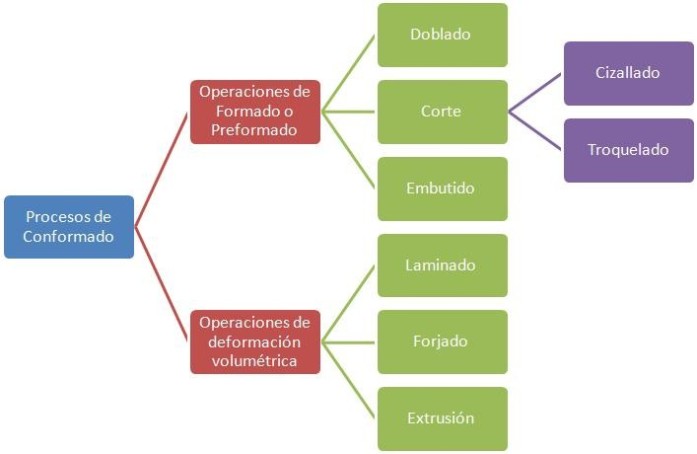
También se clasifica en:
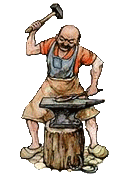
Re cristalización: Los metales que se trabajan en frío se dejan con sus granos en una condición inestable y fatigada. Los granos tienden a regresar al equilibrio en un estado más bajo de energía por la igualación de los esfuerzos internos cristalinos o cambiando a granos nuevos no fatigados. Mientras mayor sea la fatiga de deformación mayor será la inestabilidad y será más fácil que el cambio tenga lugar. El tiempo y la temperatura también influyen mucho. Ocurren dos clases de cambio: Recuperación y re cristalización, cuando se calienta un metal trabajado en frío.
El trabajo en frio se refiere al trabajo a temperatura ambiente o menor. Este trabajo ocurre al aplicar un esfuerzo mayor que la resistencia de cedencia original del metal, produciendo a la vez una deformación.
El concepto del conformado en frío comprende todos los métodos de
fabricación que permiten deformar plásticamente (a temperatura ambiente y
ejerciendo una presión elevada) metales o aleaciones de metales tales
como cobre, aluminio o latón, pero sin modificar el volumen, el peso o
las propiedades esenciales del material. Durante el conformado en frío
la materia prima recibe su nueva forma mediante un proceso que consta de
diferentes etapas de deformación. De tal manera se evita que se exceda
la capacidad de deformación del material y por lo tanto su rotura.
Las principales ventajas del trabajo en frío son: mejor precisión,
menores tolerancias, mejores acabados superficiales, posibilidades de
obtener propiedades de dirección deseadas en el producto final y mayor
dureza de las partes. Sin embargo, el trabajo en frío tiene algunas
desventajas ya que requiere mayores fuerzas porque los metales aumentan
su resistencia debido al endurecimiento por deformación, produciendo que
el esfuerzo requerido para continuar la deformación se incremente y
contrarreste el incremento de la resistencia, la reducción de la
ductilidad y el aumento de la resistencia a la tensión limitan la
cantidad de operaciones de formado que se puedan realizar a las partes.
El trabajo en caliente se refiere a procesos en los
que los metales se deforman de manera plástica por encima de su
temperatura de re cristalización. Esto es importante porque la re
cristalización mantiene los materiales de endurecimiento por
deformación, que en última instancia mantiene el límite elástico y la
dureza baja y alta ductilidad. Esto contrasta con el trabajo en frío.Temperatura
El límite inferior de la temperatura de trabajo en caliente está determinada por su temperatura de re cristalización. Como pauta, el límite inferior de la temperatura de trabajo en caliente de un material es 0,6 veces su temperatura de fusión. El límite superior para el trabajo en caliente se determina por varios factores, tales como: la oxidación excesiva, el crecimiento del grano, o una transformación de fase indeseable. En la práctica, los materiales suelen ser calentadas hasta el límite superior primero para mantener a las fuerzas que forman lo más bajo posible y para maximizar la cantidad de tiempo disponible para el trabajo en caliente la pieza de trabajo.
El aspecto más importante de cualquier proceso de trabajo en caliente es el control de la temperatura de la pieza de trabajo. 90% de la energía impartida a la pieza de trabajo se convierte en calor. Por lo tanto, si el proceso de deformación es lo suficientemente rápida la temperatura de la pieza de trabajo debería aumentar, sin embargo, esto no suele ocurrir en la práctica. La mayor parte del calor se pierde a través de la superficie de la pieza de trabajo en la herramienta de refrigerador. Esto hace que los gradientes de temperatura en la pieza de trabajo, por lo general debido a secciones transversales no uniformes, donde las secciones más delgadas están más fríos que las secciones más gruesas. En última instancia, esto puede conducir a la formación de grietas en las superficies más frías y menos dúctiles. Una forma de minimizar el problema es calentar el utillaje. Cuanto más caliente esté el utillaje, menos pérdida de calor a la misma, pero a medida que aumenta la temperatura del utillaje, la vida de la herramienta disminuye. Por lo tanto, la temperatura de las herramientas debe ser comprometida, comúnmente, las herramientas de trabajo en caliente se calienta a 500-850 F.
Ventajas y desventajas
Las ventajas son:- Disminución de la resistencia a la deformación, por lo tanto es más fácil de trabajar y usa menos energía o fuerza
- Aumento de la ductilidad
- Las temperaturas elevadas aumentan la difusión que puede eliminar o reducir inhomogeneidades químicas
- Los poros pueden reducir de tamaño o cerrar por completo durante la deformación
- En el acero, el débil, dúctil micro estructura de austenita, la cara cúbica centrada se deforma en lugar de la fuerte micro estructura de ferrita centrada en el cuerpo-cúbico encontrado a temperaturas más bajas
Las propiedades de ingeniería también se pueden mejorar mediante la re orientación de las inclusiones. En el estado fundido las inclusiones están orientadas al azar, que, cuando se cruzan la superficie, puede ser un punto de propagación de grietas. Cuando el material está caliente funcionaba las inclusiones tienden a fluir con el contorno de la superficie, creando largueros. En su conjunto las cadenas crean una estructura de flujos, donde las propiedades son aniso trópicas. Con los largueros orientado paralelo a la superficie que refuerza la pieza de trabajo, especialmente con respecto a la fractura. Las bandas actúan como “crack pararrayos”, porque la grieta se quiere propagarse a través del larguero y no por ella.
Las desventajas son:
- Reacciones adversas entre el metal y la atmósfera circundante
- Menos tolerancias precisas debido a la contracción térmica y la deformación de enfriamiento desigual
- Estructura de grano puede variar a lo largo del metal por diversas razones
Conformado según la materia prima
Los procesos de conformado plástico también se caracterizan por utilizar materiales en diferentes condiciones, ya estén o en forma de láminas o en forma de bloques masísos. Esta característica diferencia de manera particular los tipos de procesos y utilidades de cada uno.
PROCESOS QUE UTILIZAN LA MATERIA PRIMA EN FORMA DE LAMINAS: Es todo proceso de conformado de metales en donde el metal que será conformado en cierta forma determinada, se dispone inicialmente como lámina.
Dentro de este grupo, se encuentran una serie de procesos muy utilizados a nivel industrial, estos son el troquelado, doblado y embutido:
TROQUELADO:
Se denomina troquelado de metal a la operación mecánica que se utiliza para realizar agujeros en chapas en láminas metálicas. Para realizar esta tarea, se utilizan desde simples mecanismos de accionamiento manual hasta sofisticadas prensas mecánicas de gran potencia. En el siguiente link, puede observarse el proceso de troquelado en diferentes láminas: troquelado. En este vídeo puede observarse diferentes modelos de troquelado para una misma maquina de troquelado.Los elementos básicos de una troqueladora lo constituyen el troquel que tiene la forma y dimensiones del agujero que se quiera realizar, y la matriz de corte por donde se inserta el troquel cuando es impulsado de forma enérgica por la potencia que le proporciona la prensa mediante un accionamiento de excéntrica que tiene y que proporciona un golpe seco y contundente sobre la chapa, produciendo un corte limpio de la misma.
DOBLADO[2]:
El doblado de metales es la deformación de láminas alrededor de un determinado ángulo. Los ángulos pueden ser clasificados como abiertos (si son mayores a 90 grados), cerrados (menores a 90°) o rectos. Durante la operación, las fibras externas del material están en tensión, mientras que las interiores están en compresión. El doblado no produce cambios significativos en el espesor de la lámina metálica.
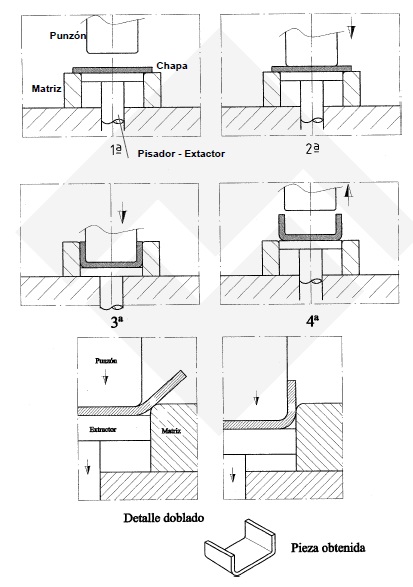
Figura 3. Fases del doblado
En el siguiente link, puede verse el proceso de doblado de una lamina
de metálica con la ayuda de un brazo robótico de la empresa KUKA: Doblamiento de lámina.
Este proceso tiene la ventaja clara de que el movimiento principal de
doblamiento lo realiza el brazo robótico, brazo en el que pueden
programarse tanto el ángulo de doblamiento como la fuerza de acción del
mismo.EMBUTIDO:
El Embutido de Chapas Metálicas es uno de los procedimientos más comunes elaboración de piezas huecas, para diversas aplicaciones que van desde el hogar, la oficina y en la industria en general. En la figura se presenta la forma que se realiza el embutido. En el siguiente link se presenta el embutimiento de pieza.
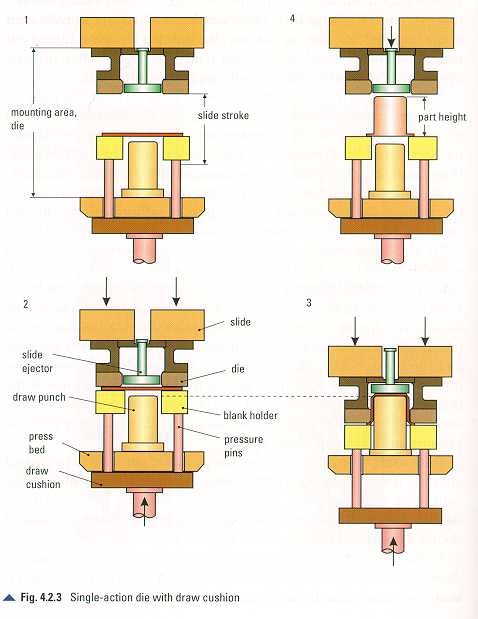
No hay comentarios:
Publicar un comentario