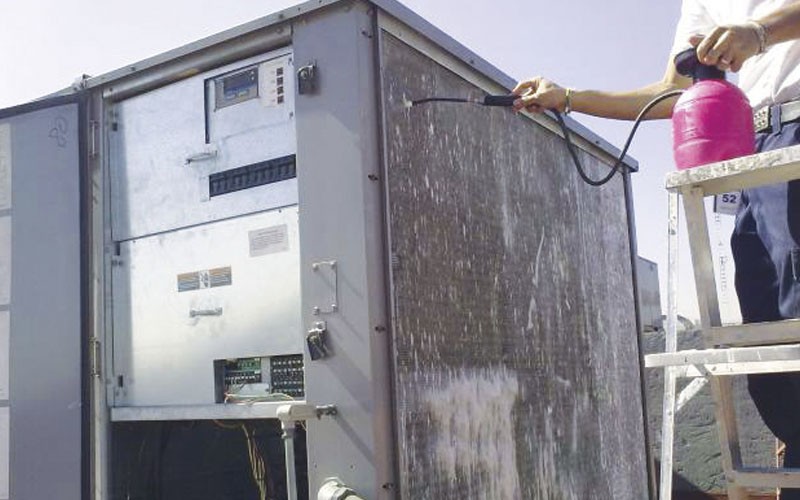
El mantenimiento es el conjunto de actividades realizadas a los sistemas HVACR con el fin de conservar el servicio para el cual fueron diseñados.
En su primera fase, es conocido como preventivo o planificado, pues tiene lugar antes de que ocurra una falla o avería. Se efectúa bajo condiciones controladas sin la existencia de algún error. También, detecta problemas en su inicio y los corrige en el momento oportuno, evitando la interrupción del servicio que proporciona el equipo de refrigeración.
Nota. No se debe perder de vista que el correcto funcionamiento de un sistema empieza siempre desde su adecuada selección y su correcta instalación
El mantenimiento preventivo presenta las siguientes características:
- Se realiza en un momento en el que no se está produciendo, por lo que se aprovechan las horas ociosas de la planta, o bien, los periodos vacacionales
- Requiere de un programa previamente elaborado, donde se detalla el procedimiento por seguir y las actividades por realizar, a fin de contar con las herramientas y repuestos necesarios
- Cuenta con fechas programadas, tiempo de inicio y término preestablecidos y aprobados por la directiva de la empresa
- Está destinado a un área y a ciertos equipos, aunque también se puede llevar a cabo un mantenimiento generalizado de toda la planta
- Permite a las empresas contar con un historial técnico de todos sus aparatos
- Requiere de un presupuesto aprobado
1. Desenergizar el equipo
2. Colocar los candados de seguridad (kit de bloqueo eléctrico) en el interruptor principal
3. Utilizar el equipo de protección personal adecuado
- Lentes de seguridad
- Guantes de nitrilo o de mecánico
- Guantes de electricista
- Zapatos de seguridad
- Candados de seguridad
Tarjeta de seguridad. Deberá colocarse en el interruptor principal o en el disyuntor de un equipo o instalación antes de empezar el trabajo de mantenimiento o reparación para evitar que sea puesto en marcha. La tarjeta llevará claramente impreso el nombre del técnico.
Candados individuales. Colocar en conjunto con la tarjeta de seguridad. No la reemplaza. Los candados deberán tener la identificación del técnico y sólo podrán ser retirados junto con la tarjeta. La llave del candado quedará en poder del técnico.
Candados multihoyos. Empleados cuando varios especialistas intervienen en el mismo equipo. Todos cerrarán un orificio con candados individuales. Una vez que el trabajo haya terminado, todas las llaves individuales serán retiradas. De igual manera, cada técnico deberá colocar su tarjeta de seguridad.
Protocolo de mantenimiento preventivo
Evaporador
1. Limpieza general del gabinete
2. Lavado del serpentín de evaporación, utilizando un producto químico especialmente formulado para desengrasado y desinfección
3. Peinado de las aletas del serpentín del evaporador
4. Verificar que el bulbo sensor de la válvula termostática de expansión se encuentre en la posición correcta, sujeto firmemente a la tubería y perfectamente aislado
5. Confirmar que la VTE tenga correctamente conectado el igualador de presión externo
6. Limpieza de los motores y sus aspas
7. Desinfección de la charola de condensados
8. Limpieza del dren de condensados
9. Para evaporadores con deshielo por resistencias, verificar las resistencias del serpentín, de la charola de condensados y del dren
10. Cotejar que el termostato de cuarto esté conectado eléctricamente en serie con la bobina de la válvula solenoide de líquido
11. Reapretar tornillería y, en su caso, colocar los faltantes
12. Ajustar conexiones eléctricas
13. Revisar cableado externo
14. Revisar cableado de control
Condensador
1. Limpieza general del gabinete
2. Lavado del serpentín de condensación. Se debe evaluar, dependiendo de las condiciones, el uso de un producto químico
3. Desinfección de los motores y sus aspas
4. Reapriete de tornillería; de ser necesario, colocar los faltantes
5. Ajuste de conexiones eléctricas
6. Revisión del contactor y, en su caso, limpieza de platinos
7. Verificación o corrección de la presión de paro (cut out) del control de baja presión del compresor
8. Verificación o cambio del aislante de la tubería de succión
9. Comprobación o ajuste de sobrecalentamiento del sistema
10. Revisión del correcto funcionamiento del calefactor del cárter
11. Chequeo del cableado externo
12. Corroboración del cableado de control
13. Toma de amperaje a plena carga y comparación con los datos de placa
Nota. Generalmente, el consumo de amperaje debe ser aproximadamente del 70 al 80 por ciento del valor del RLA (amperaje a plena carga)
Nota. Debemos tomar en cuenta que el mantenimiento preventivo no sólo involucra la limpieza del equipo y verificación de la carga de refrigerante; además, elimina los factores que pueden provocar fallas para no llegar a la fase de mantenimiento correctivo
Factores por considerar
A continuación se revisarán algunos aspectos que se deben cubrir en los sistemas de refrigeración y que ayudarán en campo a tomar las decisiones pertinentes para que los equipos operen en condiciones adecuadas.
Bombeo completo. Funcionará de forma correcta si la válvula solenoide de líquido se instala lo más cerca que se pueda a la válvula de expansión termostática. Cuando el termostato de cuarto detecta la temperatura interior a la cual fue calibrado, interrumpirá la energía de la bobina de la válvula solenoide de líquido, provocando que cierre. Al no haber paso de refrigerante, la presión de succión disminuirá hasta el valor de presión de paro (cut out) del control de baja presión del compresor (presostato), lo que desenergizará la bobina del contactor del compresor, provocando su paro.
En este punto, se dice que el compresor realizó el barrido casi completo y paró debido a presión positiva por arriba de 0 Psig. Es muy importante tener en cuenta que un compresor nunca para por vacío, ya que el vacío significa que el compresor se está deteniendo a presiones por debajo de 0 Psig. Parar un compresor a estas presiones es llevarlo directo a una falla prematura.
Válvula termostática de expansión. A fin de compensar una caída de presión excesiva a través del evaporador, sobre todo cuando se tienen distribuidores de refrigerante, la válvula de termoexpansión debe de contar con igualador externo, con la línea del igualador conectada a la de succión, junto al bulbo remoto del lado del compresor. Como un método práctico, la línea del igualador deberá conectarse a la de succión a la salida del evaporador. Si se utiliza una VTE con igualador externo, con la línea del igualador conectada a la de succión, se ejercerá la verdadera presión de la salida del evaporador debajo del diafragma de la VTE. Las presiones de operación sobre el diafragma de la válvula están libres de cualquier efecto de caída de presión a través del evaporador, y la válvula responderá al sobrecalentamiento del refrigerante que sale del evaporador. Es muy frecuente encontrar sistemas a los que se les eliminó el igualador externo; como parte del servicio, es importante realizar la correcta conexión del igualador.
Deshielo en las madrugadas o con temperaturas ambientales bajas. Es común que el evaporador se vuelva el elemento más caliente del sistema de refrigeración cuando entra en periodos de deshielo, en días con bajas temperaturas ambientales o normalmente durante la madrugada. Este hecho originará que el refrigerante líquido en el evaporador tienda a fluir hacia la línea de succión y hacia el compresor (que se vuelve el cuerpo más frío del sistema de refrigeración), y cuando éste arranque lo haga de forma inundada, lo cual algunas veces provocará que se active el control de presión de aceite, desencadenando que el compresor se proteja. Esto revela por qué, en ocasiones, el compresor se encuentra protegido en la mañana o a ciertas horas del día sin explicación aparente.
Deshielo por resistencia eléctrica. A juzgar por los reportes de fallas en compresores, la principal causa de éstas se debe a la cantidad excesiva y descontrolada de refrigerante líquido que regresa al compresor. La mayoría de las veces, es provocada por los ciclos de deshielos que son necesarios para la limpieza del serpentín del evaporador. Una de las principales recomendaciones es usar el bombeo completo mediante un acumulador de succión con la capacidad de almacenamiento suficiente para retener el refrigerante líquido proveniente del evaporador, evitando que entre directamente en el compresor. Para deshielos por resistencias eléctricas, el acumulador de succión que se instala de fábrica en las unidades condensadoras es de diseño de capacidad estándar, suficiente para retener el refrigerante líquido cuando se usa el bombeo completo.
Deshielo por gas caliente. Proceso que se vuelve crítico cuando se trata de un sistema de refrigeración formado por una unidad condensadora y un evaporador, debido a que, cuando entra el ciclo de deshielo, el compresor continúa funcionando y una gran cantidad de refrigerante en estado líquido regresa directamente a él, lo que en muchas ocasiones provoca que funcione de forma inundada, originando la dilución del aceite lubricante y, a su vez, una lubricación deficiente de las partes internas del compresor. Este regreso excesivo de refrigerante líquido, algunas veces, puede provocar la activación del control de presión de aceite, debido a la baja presión de lubricación en el cárter del compresor. En muchos de los casos, desafortunadamente, la bomba de aceite (caso de compresores semiherméticos) manejará una gran mezcla de refrigerante líquido-aceite lubricante y desarrollará suficiente presión para evitar que el control de presión de aceite se active. Esto provocará una lubricación inadecuada que conducirá a una falla prematura del compresor. La cantidad de refrigerante líquido de retorno hacia el compresor dependerá del tamaño de la unidad condensadora (compresor) y del recorrido de tuberías entre el evaporador y la unidad condensadora.
Algunas de las soluciones que se deben tomar en cuenta para sistemas de unidades condensadoras con sus respectivos evaporadores son emplear una válvula reguladora de presión de succión del compresor (crankase pressure regulator, CPR) y un acumulador de succión de capacidad estándar. En su defecto, se deberá utilizar un acumulador de succión de capacidad considerable, acompañado de alguna fuente de calor para re-evaporar el refrigerante líquido y proteger al compresor.
Para deshielos por gas caliente en sistemas con unidad condensadora, el acumulador de succión que se instala de fábrica cuenta con diseño de capacidad estándar; adecuado, si se usa en conjunto con una válvula reguladora de presión de succión del compresor (CPR).
Retorno de refrigerante líquido. Este problema se agudiza a medida que crece el sistema. Las razones son:
1. Recorridos de tuberías demasiado largos
2. Sobrecarga de refrigerante
3. Equipos seleccionados incorrectamente
4. Calefactor del cárter en mal estado
5. Ausencia de bombeo completo
6. Motores ventiladores de los evaporadores defectuosos
7. Evaporador con demasiada escarcha provocada por infiltraciones, tiempos muy cortos en los periodos de deshielo o acumulación en la charola de condensados
8. Válvula de expansión termostática incorrecta, normalmente sobredimensionada o mal ajustada (sobrecalentamiento incorrecto)
9. Diámetros de tuberías incorrectos y más
Presión de descarga o de condensación. Para determinar si la presión de descarga que se tiene en el sistema es la adecuada, se debe consultar en las Tablas de Temperatura de Diseño para la República Mexicana de la Asociación Mexicana de Empresas del Ramo de Instalaciones para la Construcción, A.C (AMERIC), o en el Manual de Ingeniería de BOHN, la temperatura de diseño para la ciudad de la República donde estemos ubicados. A esa temperatura se le sumarán 15 ºC y se obtendrá la temperatura de condensación. El siguiente paso es ir a la tabla de presiones de refrigerante y leer la presión que corresponde a esa temperatura para el refrigerante que se tiene en el sistema.
Ejemplo. Equipo instalado en la Ciudad de México que utiliza R-22, la temperatura de diseño es de 32 ºC, la temperatura de condensación será de TC= 32 + 15 = 47 ºC. De las tablas de R-22, leemos para 46.7 ºC una presión de 246.1 Psig, lo cual nos indica que esperamos presiones de condensación como máximo de 246 Psig.
Temperatura de descarga del compresor. Se mide la temperatura sobre la tubería de descarga del compresor a una distancia de 15 centímetros de la válvula de descarga del compresor; la temperatura medida indica lo siguiente:
107 ºC = Operación normal
121 ºC = Peligro de falla
135 ºC = Falla segura
Sobrecalentamiento. Definido como la diferencia entre la temperatura medida a la salida del evaporador y la temperatura de la tabla P/T de los refrigerantes; es decir:
1. Se determina primero la presión de succión mediante la lectura del manómetro a la salida del evaporador. En instalaciones pequeñas o en equipos autocontenidos, la medición se puede hacer en la conexión de succión del compresor
2. De las tablas P/T, se determina la temperatura de saturación a la presión de succión observada
3. Se toma la lectura de la temperatura de la tubería de succión lo más cerca posible del bulbo sensor de la VET
4. Se resta la temperatura de saturación leída de las tablas en el paso 2 a la temperatura leída en el paso 3. La diferencia es el sobrecalentamiento del gas de succión
El sobrecalentamiento es la condición en la cual el refrigerante está completamente evaporado; es decir, si se tiene un proceso correcto, se va a lograr que el equipo opere eficientemente y, además, no va a existir el riesgo de que regrese líquido al compresor, ya que todo el gas que regrese va a estar en fase de vapor.
El sobrecalentamiento recomendado, según la aplicación a la salida del evaporador, es:
Para alta temperatura: Temperatura de evaporación= 0 ºC o mayor; el sobrecalentamiento debe estar entre los 6 y los 7 ºC
Para temperatura media: Temperatura de evaporación= -18 a 10 ºC; el sobrecalentamiento debe ubicarse entre los 3 y los 6 ºC
Para temperatura baja: Temperatura de evaporación= debajo de -18ºC; el sobrecalentamiento debe situarse entre 1 y 3 ºC
No hay comentarios:
Publicar un comentario