En muchas ocasiones no se presta suficiente atención al efecto de las desviaciones geométricas de las herramientas de corte en la precisión final de las piezas producidas. Desde el punto de vista de la precisión alcanzable en una pieza a fabricar, la tendencia en una cadena de manufactura es pensar desde la herramienta hacia adelante, sin tener en cuenta que esta también tuvo que ser fabricada de alguna manera.
En el caso de las herramientas de carburos cementados, después de un proceso de sintetizado, los filos son pre-cortados por electroerosión de hilo y afilados finalmente mediante procesos de rectificado. En un paso final, las herramientas de corte pueden ser recubiertas con una o varias capas de diferentes compuestos para mejorar su rendimiento. Toda esta cadena entrega finalmente un determinado valor de tolerancia geométrica, que en ningún caso es igual a cero.
Por otro lado, los insertos de corte, siguiendo la norma ISO 1832-1991 que rige su nomenclatura, la tercera posición en el código de cada uno de ellos, se refiere al tipo de tolerancias dimensionales que tiene el inserto mismo. Se pueden conseguir herramientas de tipo A, con tolerancias que van entre ± 5 y 25 µm, hasta insertos con tolerancia de tipo U, que en tamaños superiores a los 25 mm pueden tener tolerancias entre los 250 y 380 mm. ( Ver Diagrama 1)
Cuando se trata de herramientas sólidas, como fresas o brocas, además de la tolerancia del diámetro de corte, que se encuentra normalmente en valores de -20 a -60 µm para herramientas de más de 3 mm, se deben revisar los valores de concentricidad del eje que a su vez llegan a ser de 10 a 20 µm. Herramientas de mayor precisión, pueden alcanzar valores de tolerancia en el diámetro y de concentricidad por debajo de 5 µm, aumentando su costo, pero también la seguridad de que la pieza saldrá de la máquina cumpliendo las tolerancias especificadas.
Todas estas tolerancias, más otras que deben ser informadas por los vendedores de herramientas, como la del radio de la punta de la herramienta en escariadoras, o del radio de la esfera en fresas de bola, suman a la incertidumbre de la medición final de la pieza que se quiere fabricar. Y por esto es necesario instalar equipos de verificación geométrica de herramientas en el taller. Dentro o fuera de la máquina, dependiendo de la productividad del proceso, pero sin este paso, se está perdiendo gran parte de la información necesaria para obtener un producto de buena precisión.
Pero de nada sirve tener excelentes herramientas si la máquina que las utiliza no tiene buena precisión de posicionamiento y la robustez estática y dinámica que garantice que las piezas fabricadas van a tener una buena calidad.
La empresa F.V. – Área Andina S.A. fabricantes de grifería, sanitarios y complementos con sede en Quito, Ecuador, es un excelente ejemplo de la aplicación de buenas prácticas de manufactura mediante la combinación de maquinaria de última tecnología con herramientas de excelente calidad.
Incluso capaces de fabricar sus propias herramientas especiales de carburos cementado
Con la puesta en marcha de nuevas máquinas multitarea basadas en torno de Mazak, se han logrado mejoras de productividad de hasta un 50% en aplicaciones para piezas de latón para grifería, mediante el uso del doble husillo y la doble torreta, haciendo 10 procesos en una misma máquina. Este proceso reemplaza el trabajo hecho anteriormente en dos máquinas separadas. Miguel Pantalano, gerente de la planta de grifería de F.V. asegura que “los costos claves en este negocio son el minuto productivo y el costo de la materia prima. Al reducir tiempos muertos al no tener que pasar de una máquina a otra, tener mayor velocidad y menor cantidad de operaciones, se logra mayor versatilidad para productos complejos y se logra capacidad para sacar piezas casi listas, reduciendo así costos clave.” ( Ver Figura 2 )
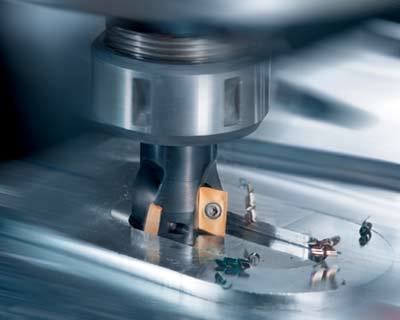
No hay comentarios:
Publicar un comentario